Aecon Field Operating System

Aecon is Canada’s largest publicly traded construction and infrastructure development company servicing private and public sectors both in Canada and Internationally. Aecon’s diverse capabilities include: infrastructure, civil, utilities, buildings, industrial and nuclear sectors.
Client Profile:
Industry:
Construction and infrastructure development
Services:
Aecon’s services range from financing, design, construction and operations to procurement, materials, engineering and fabrication.
Established:
Established in 1910, Aecon was listed on the TSX in 1987.
Market Capitalization:
The aggregate value of Aecon is close to $ 224 Million CAD.
Situation:
As one of the largest and most diverse construction and infrastructure developers in Canada, Aecon found that they needed a Field Operating System that would keep track of work orders, facilitate the scheduling and billing of work orders and to achieve efficiencies by putting the automation of the system out into the field.
Aecon started investigating the automation of FOS as early as 1998, as a stand-alone system to manage work orders. However, Aecon’s business has developed and expanded geographically, as had the need for greater automation, integration and distribution of technology.
Aecon recognized that the manual collection and entry of daily construction-project data was becoming burdensome, that it required too much staff time to separately record and enter data. It was hampering Aecon’s ability to both manage projects effectively and turn around payroll and billing efficiently. Aecon approached Sundex to build a scalable solution that would develop over time to enhance productivity, create cost-savings and improve project throughput.
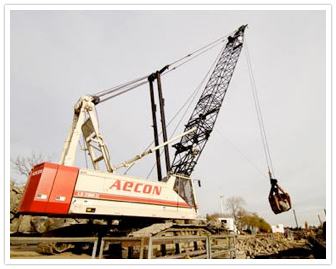
Solution:
Part One: Work Order Tracking
Between 1998 and 2001, Aecon contracted and jointly designed a work order tracking system with Sundex. The solution began as a system to allow office-based Aecon employees to add, remove and update work orders. Further development of the project saw a roll-out of mobile computers, or personal data assistants (PDAs) to the foreman in the field to allow them to update and modify work orders remotely. The PDAs are synchronized with the work order tracking system at the end of each day. Aecon dubbed this field operating system FOS 2001.
Part Two: FOS Mobile
FOS PDA
The name given to the project to increase the mobile use of FOS 2001 on the PDAs was FOS PDA. In addition to allowing foremen to see work orders, this mobile aspect of FOS allowed them to receive downloaded schedules as well as employee, safety and equipment information. Once downloaded, foremen could enter employee time, client work, equipment readings and safety updates. At the end of each work-day, the PDA is synchronized with the FOS system to update the FOS database with information. Ultimately Aecon would integrate with their back-office to have that information flow through to the back office, and to subsequently receive updates back to the PDA from FOS. The mobile aspect of FOS gave greater capability to the field, it reduced reporting times and created efficiencies in delivering schedule, work order and equipment changes on a just-in-time basis.
FOS Web
In addition to extending the field capability through the PDA, Sundex developed a web-based mobile module of FOS allowing Aecon’s customers to approve work orders over the Internet through a web interface.
Part Three: Integration
Internal Systems Integration
Once the work order tracking system was developed and rolled-out to their users, Aecon discovered a need to integrate FOS with their back office to create even greater efficiencies through automation.
To integrate FOS with the back-office, Sundex and Aecon developed an interface into Aecon’s Construction Management System or CMS. By developing a successful flow through of data from the field to CMS, Sundex was able to give Aecon the ability to automatically update employee hours, employee allowances, and to issue both payroll and client billing directly from FOS through CMS. This solution has been further developed to include Aecon’s Civil division requirements.
External Systems Integration: B2B
The successful integration of CMS gave Aecon the confidence to extend the FOS System to integrate with business partners. Union Gas approached Aecon with a request to automate the receipt or exchange of work between them. Sundex created a web-services Business-to-Business solution to exchange XML entries between the two entries in a completely secure fashion, without requiring Aecon or Union Gas to have direct access to each other’s internal systems.
Four: FOS Reporting
The final component of the FOS System was the requirement to provide detailed, customized reports for Aecon to help them manage their business, to look at historical information and to provide a basis for analysis and business intelligence. Sundex delivered this capability through a variety of dynamic reports.
The Business Benefit:
The original objective of a work order tracking system set by Aecon was achieved. They were able to provide automation for their work force tracking work orders in the field and to subsequently gain efficiencies in billing, payroll and reporting.
Efficient tracking of work orders was achieved through all stages of the process. Turn-around time and accuracy of input also reduced the amount of time and man power required to do data entry and to reconcile and correct issues.
By adding additional functionality in integration, mobility and reporting, Aecon has been able to extend similar efficiencies to business partners such as Union Gas, and other divisions of Aecon including their Civil division and QX Locates.
The system has facilitated greater accuracy as well as increased business volumes. Similarly, accurate and more timely business information allows for better and more flexible decision making.
The ancillary benefits of this system have resulted in increased quality, robustness and accuracy of data. It has enhanced Aecon’s workforce in that staff are spending less time on mundane repetitive tasks and in error correction and more time on higher-quality work activities.
Finally, Aecon has a successful, robust automation facility that will continue to help them meet their strategic business objectives.